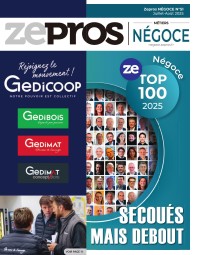
Béton & ciment : la filière se met au vert
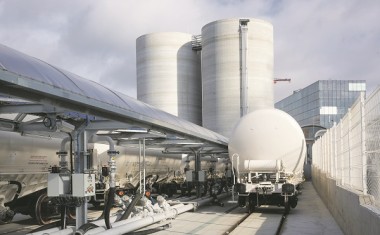
[Zepros Bati] Face à des ressources qui s’épuisent et des réglementations qui se font de plus en plus exigeantes, les industriels du ciment et du béton cherchent toutes les solutions possibles pour réduire leur empreinte environnementale. Évolution des procédés industriels, mise au point de formulations alternatives, transformation de déchets en ressources... les pistes explorées sont nombreuses. Dossier réalisé par G.Noble et M.Wast.
En avril 2016, les exploitants de carrières de granulats (Unicem) et les spécialistes du béton (SNBPE) signaient avec l’État un des tout premiers « Engagements pour la croissance verte » (ECV), afin d’intensifier la démarche de valorisation et de recyclage des déchets inertes du BTP. Plusieurs objectifs étaient alors définis : une utilisation rationnalisée des ressources, le développement de la reprise des matériaux issus des déconstructions, avec en ligne de mire un taux de 70 % de recyclage fixé par l’Union européenne. Trois ans plus tard, toute la filière affiche avec satisfaction une proportion de 80 % de matériaux inertes recyclés, couvrant 28 % des besoins en granulats pour la construction. Des chiffres obtenus grâce au réemploi direct sur les chantiers de Travaux publics, au recyclage par des plateformes dédiées et à la valorisation dans des remblais de carrières.
Caractériser les matériaux
Les offres se multiplient
Transformer les sédiments fluviaux en matériau fiable
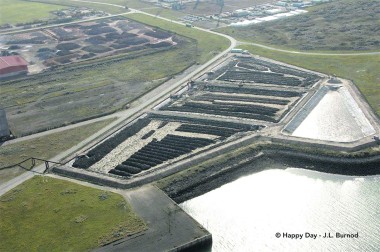
Valoriser les terres polluées des friches industrielles
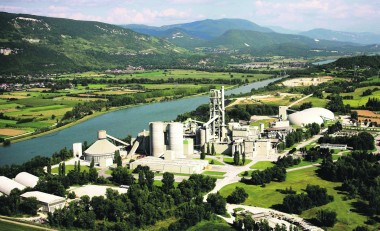
Des centrales à béton “zéro rejet” pour le Grand Paris
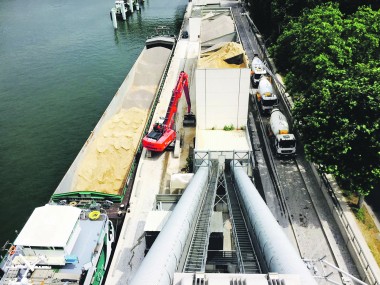
Matériaux naturels et recyclage
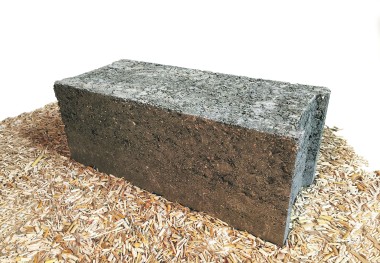
Sur le même sujet
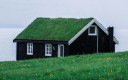
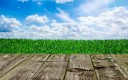
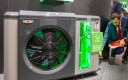
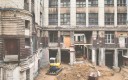

