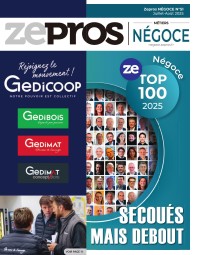
Construction hors site et modulaire : c'est dans la boîte !
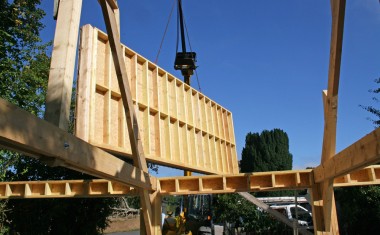
Elle suscite de nombreuses craintes à beaucoup et stimule l’imagination de bien d’autres… La construction hors site sort peu à peu de l’ombre et compte bien gagner ses lettres de noblesse dans un contexte réglementaire qui met la performance et l’environnement en tête des préoccupations. Explications.
La construction hors-site est un mode constructif qui permet de fabriquer et de pré-assembler des composants de bâtiments, en usine, pour une installation sur l’emplacement définitif. Elle est issue du DFMA - Design for Manufacturing & Assembly -, “Concevoir pour la Préfabrication et l’Assemblage”. Cette méthode “différente” de construction intègre, dans un processus industriel original, tous les métiers du bâtiment et impose à l’ensemble de la filière de se réinventer et d’adapter ses méthodes. En pleine croissance, la construction hors-site devrait représenter d’ici 2030, 20 % des bâtiments construits dans le monde (source Cabinet McKinsey). Pourtant elle ne date pas d’hier, puisqu’avant d’être plus globale, on parlait de préfabrication, surtout dans les domaines du béton et du bois, par exemple. D’ailleurs, les acteurs de ces filières ont pris une longueur d’avance depuis de nombreuses années, ce qui a permis de peaufiner et rendre encore plus performants les process de production.
Révélée par la réglementation RT2012, la construction modulaire et hors-site a tous les atouts pour relever les défis de la loi Climat et Résilience du 22 août 2021. Alors que le secteur du bâtiment engendre 70 % des déchets en France et l’équivalent d’un million de m2 de destruction de matériaux, une réflexion sur des bâtiments durables, réversibles et reconditionnés s’impose. « La loi Climat et Résilience, en favorisant le réemploi des matériaux dans le secteur de la construction, concrétise la prise de conscience des pouvoirs publics sur l’intérêt, en matière d’impact carbone, de cette pratique », affirme Pierre Visonneau, directeur général de Deltamod. L’entrée en vigueur de la RE2020, qui vise à améliorer les performances énergétiques et le bilan carbone des bâtiments neufs, oriente les promoteurs et les investisseurs vers des technologies bas carbone et énergétiquement sobres. De fait, la circularité du mode de construction modulaire et la réversibilité des bâtiments sont les principaux leviers de ce nouveau marché qui ne représente, aujourd’hui, que 1 à 2 % de la production immobilière. « La RE2020 a fait bouger les lignes en obligeant les acteurs de la construction à changer de paradigme. La révolution industrielle se fait pas à pas et la réflexion sur les concepts hors-site et modulaires s’inscrit dans un temps long », ajoute Éric Aurenche.
Le moment ou jamais
En butte à des problématiques structurelles (atomisation du marché, dégradation des prix, difficultés à recruter…), le secteur de la construction doit pourtant satisfaire des besoins accrus en logements. Alors que la France compte déjà 4 millions de mal-logés (Source Fondation Abbé Pierre) et qu’il manque 2 millions de logements environ, notre pays devrait accueillir 2 millions de ménages supplémentaires entre 2022 et 2030. Il faudrait donc doubler la production annuelle de logements en 8 ans. Face à cette urgence, l’industrialisation de la construction hors-site est une opportunité de produire plus et plus vite des logements collectifs. Mais cette impulsion ne pourra être donnée que par les élus locaux qui œuvrent sur le terrain et ouvrent la voie aux promoteurs. « Dans un contexte de raréfaction de la main d’œuvre, de pénurie de logements et de verdissement des politiques locales, c’est le moment ou jamais pour les acteurs du hors-site de prendre la place qui leur est due dans le débat politique pour que les pouvoirs publics intègrent ce mode constructif dans leur plan de réindustrialisation du territoire », déclare Vincent Pavanello, co-fondateur du think tank Real Estech.
La clé de la massification
Située au carrefour de l’industrie et du bâtiment, la construction hors-site et modulaire a sa carte à jouer pour un immobilier plus propre. « Elle coche toutes les cases d’un mode constructif vertueux », résume Christophe Cougnaud, directeur général de l’entreprise éponyme. Pour transformer le parc de "passoires thermiques" en immeubles à énergie zéro avec de la rénovation industrialisée ou concevoir des bâtiments intégrant le cycle de fin de vie, les entreprises doivent adopter une démarche d’industrialisation et massifier leur production afin de bénéficier d’économies d’échelles et de processus plus homogènes et fluides. « Il faut sortir d’une vision à l’affaire pour entrer dans une logique de production à grande échelle », assure Pascal Chazal, CEO de Patch Conseil.
Dossier réalisé par Jérémy Becam, Grégoire Noble et Marc Wast. Sources Acim, Avelis et BTP Consultants.
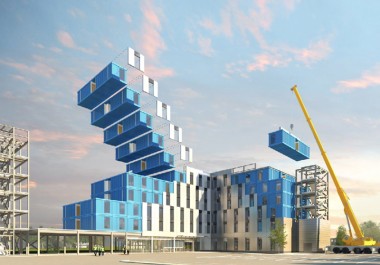
Un référentiel pour accélérer
Avec l’appui du Centre Scientifique et Technique du Bâtiment (CSTB), le syndicat des Acteurs de la Construction Industrialisée et Modulaire (ACIM) viennent de mettre en place un référentiel de certification qui permettra à la construction modulaire d’offrir les mêmes critères d’assurabilité que la construction traditionnelle et de démontrer que la conception hors-site s’inscrit dans la durée. « Du chemin a été parcouru depuis 5 ans et les mentalités ont évolué sur la construction modulaire. Grâce au nouveau référentiel de certification délivré par le CSTB, nous pourrons passer d’une prospective inspirante à des actions au quotidien. Cet objectif se concrétise aujourd’hui avec l’Acim », a annoncé Éric Aurenche, président de l’Acim.
Quelques chiffres
5,5 % : L’augmentation des coûts de la construction entre 2019 et 2021 en France (Source Insee)
19,3 % : la baisse cumulée de la productivité sur les chantiers depuis 2001 (Source Xerfi)
1,5 Md€ : l’estimation des produits et matériaux non utilisés sur les chantiers français
75 % : la hausse de la sinistralité sur les 10 dernières années (Source SMABTP)
Matériau Bois : En rénovation aussi, la préfabrication s'impose
La démarche EnergieSprong, née aux Pays-Bas, vise à massifier la rénovation thermique à zéro énergie (sur 30 ans) au moyen de l’industrialisation des chantiers. En France, près de 2 500 logements dans le collectif ont déjà été rénovés, en plus de 1100 maisons individuelles. Le bailleur social Plurial Novilia (groupe Action Logement) très impliqué dans les innovations expérimentales, a choisi de mener la réhabilitation de 127 logements lui appartenant à Reims grâce à des panneaux isolants de bois. Le procédé, développé par la société Techniwood, se nomme Panobloc et se présente comme une façade de 200 mm d’épaisseur, doublée de laine de roche, préfabriquée en usine et assemblée sur site. La structure de bois, composée de CLT, est travaillée en atelier, où sont adjoints le revêtement extérieur en bardage et les menuiseries. Livrés tout équipés, les panneaux sont montés rapidement, sur un chantier aux nuisances réduites.
Le résultat : un gain de 20 à 30 % sur la performance thermique, avec la suppression de tous les ponts thermiques et une meilleure étanchéité face aux éléments. Les logements passent ainsi d’une étiquette « F » ou « E » à une étiquette « C », avec une réduction des consommations énergétiques de l’ordre de 40 % qui permet de financer les travaux. Alain Nicole, le directeur général de Plurial Novilia, fait valoir : « Les travaux de réhabilitation que nous menons visent à la fois à améliorer le confort des habitants et la performance du bâti. Pour autant, ce sont des chantiers conséquents, menés en sites occupés, et qui d’ordinaire s’étalent sur de longs mois, pouvant créer de vraies tensions pour les occupants. Nous cherchons donc en permanence à améliorer nos chantiers grâce à des solutions innovantes ».
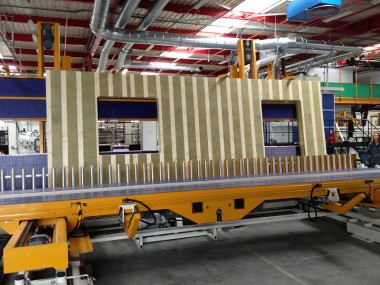
Matériau Béton : la construction bas carbone passe par la "Préfa"
Comme les autres matériaux, le béton fait valoir ses arguments pour le respect de la RE2020 qui vise à diminuer l’empreinte carbone des bâtiments tout en maintenant leur performance thermique. Mais le béton est gourmand en ressources et en énergie, le ciment qui le constitue étant fortement générateur de CO2. Des solutions existent bel et bien, dans la chimie d’abord pour réduire les émissions de carbone liées à sa production, mais également dans sa mise en œuvre. Le groupe KP1 notamment met en avant les avantages de la précontrainte qui confère aux poutres ou prédalles « des caractéristiques hautement performantes de résistance et de portée », de sorte que pour un même résultat, il y aura besoin de moins de matériau. Une poutre de béton armé simple de 45 x 30 cm peut être avantageusement remplacée par une poutre en béton précontraint de 30 x 25 cm (-40 %). De même, une prédalle précontrainte économisera 25 % de CO2, passant de 24 kg/m² à moins de 18. Les structures porteuses se font légères et fines, se font plus simples à mettre en œuvre.
La fabrication en usine permet donc d’optimiser le dimensionnement des éléments, d’en contrôler la qualité en continu, et de générer moins de déchets. Outre les planchers, poteaux, poutres et escaliers, sont apparus de nouveaux éléments modulaires complets dits « monoblocs tridimensionnels ». Patrick Soubiran, directeur commercial CIR-Préfa, explique sur Infociments : « Nous devenons des équipementiers, en intégrant à la structure béton l’équipement électrique, la plomberie, les revêtements de sols ou murs, voire le mobilier ! Nous intégrons de nouvelles compétences, tant en usine que sur site, puisque nos équipes assurent le montage des éléments afin de garantir la meilleure précision dans l’ajustement des modules ». Le chantier s’en trouve raccourci et simplifié, avec moins de nuisances. Ainsi, il est possible de venir procéder à l’extension d’immeubles existants en empilant des modules par l’extérieur qui contiennent loggias et circulations verticales, à raison d’un étage par jour, en site occupé.
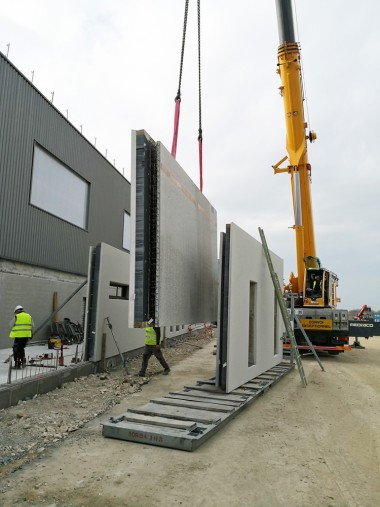
Matériau Acier : la construction métal s'incrit dans le "100 % made in France"
Lancé en avril 2021 par ArcelorMittal, le label Véritube permet d’identifier la provenance et la qualité de tubes en acier fabriqués en France (sites de Lexy, Fresnoy, Rettel ou Vincey), depuis la bobine d’acier jusqu’au produit fini. Le groupe Cougnaud, qui développe un procédé constructif hors site l’a choisi pour sa démarche de qualité environnementale. Chaque année, ce groupe construit 220 000 m² de surfaces de bâtiment, utilisant au passage 8 000 tonnes de tubes d’acier. Jean-Yves Cougnaud, directeur général Achats, précise : « Depuis 50 ans, le groupe a forgé sa réputation sur l’innovation et la qualité de son mode constructif. Avec les tubes Véritube, nous nous assurons un approvisionnement de proximité auprès d’un des leaders du marché tout en contribuant au rayonnement des savoir-faire industriels français ». Ce sont ainsi 800 t de tubes labellisés qui ont été commandées en 2021.
Cougnaud est notamment impliqué dans la construction pour Solideo d’un foyer de travailleurs migrants à Saint-Ouen (93) dans le cadre plus vaste du futur chantier du village des athlètes des JO2024. « Afin de respecter les délais, Solideo a privilégié une solution de relogement temporaire, avec un emménagement sous 6 mois et sur une durée de 2 ans, dans l’attente de la construction de deux résidences sociales sur la commune ». Le bâtiment devait également pouvoir être démonté puis remonté sur un autre site, ce qui a amené à une solution modulaire. Le projet de 6 300 m² sur 4 niveaux incorpore 224 studios équipés et de vastes espaces communs. Délai d’exécution : 6 mois.
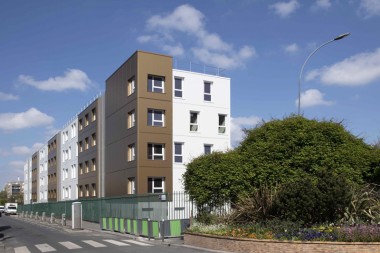
De l'habitat modulaire à l'habitat exemplaire
La construction modulaire va peut-être réinventer le concept même de maison. Citygie, fabricant d’éléments en béton, annonce travailler sur une offre d’habitat modulaire durable. Éric Piroud, le dirigeant, annonce : « Ces modules en béton sont fabriqués dans notre usine de Chaleins (Ain). Nous réaliserons dès le début de l’année prochaine un démonstrateur habitable : une maison individuelle sera préfabriquée et prémontée en usine avant d’être installée sur site ». La première réalisation devra permettre d’obtenir un avis technique du CSTB sur la solution constructive. « La préfabrication fait maintenant valoir ses atouts durables », poursuit-il. « Fabriquer en atelier ‘hors-site’ permet d’alléger l’impact de la construction sur l’environnement immédiat par la réduction des nuisances sonores et de circulation et par une consommation moindre de matériaux ». Citygie promet également la réversibilité des bâtiments que ce soit dans les usages ou dans la localisation.
Autre exemple, celui de Podeliha (groupe Action Logement) qui lance sa marque Habiflex de « logements déplaçables et transitoires ». Il repose sur des habitations modulaires préconstruites et assemblées sur place, livrées en moins d’un an et louées pour une période de 7 ans maximum. La solution offre l’avantage d’utiliser temporairement le terrain d’une collectivité pour accueillir rapidement des familles en attente d’un logement. Les modules en bois sont assemblés par 2, 3 ou 4 pour constituer une habitation. À Chanverrie (Vendée), c’est l’entreprise LECO2 et le cabinet S.Mart Architecture qui prendront en charge le projet, de la conception jusqu’à l’assemblage de 20 maisons de 63 m². Podeliha souligne : « Concrètement, cette solution de logements est développée grâce à une technologie aux performances énergétiques exemplaires dont l’empreinte écologique est maîtrisée : matériaux biosourcés, production locale, fabrication hors site à 90 %, temps de transport réduit, maîtrise du cycle des déchets, chantier à faible nuisance, réemploi possible à 95 % des matériaux de la phase temporaire ». Montant du loyer ? Environ 350 € hors charges pour des logements au standard RE2020 (avec PAC air/eau et radiateurs à eau chaude), classés E2C2 et Bâtiment Biosourcé niveau 3.
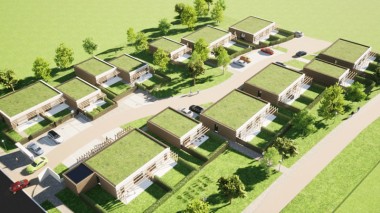
Des salles de bains préfabriquées mais personnalisées
Les salles de bains sont un candidat idéal pour la construction hors-site car ce sont des unités relativement petites et autonomes. Il s’agit d’une technologie optée depuis des années notamment par les chaines hôtelières afin de réduire les coûts, améliorer la qualité des finitions et la sécurité sur chantier. Dans le cadre d’un projet de construction, une multitude de corps de métiers sont mobilisés dans la conception de la salle de bains : plombiers, électriciens, carreleurs, soliers, menuisiers et autres spécialistes. Cela nécessite un grand effort de supervision et d’encadrement pour assurer un séquençage et la qualité des travaux. De plus en plus d’entreprises générales ont tendance à créer leur propre entreprise de fabrication comme Eiffage qui a développé HVA concept pour les salles de bains modulaires volumétriques complètement préfabriquées et préfinies à l’usine. « En une seule pièce, nous emmenons l’ensemble de la salle de bains sur le chantier. C’est facilitant pour le chantier parce qu’il y a qu’un seul interlocuteur donc la coordination est beaucoup plus simple. Nous concentrons tous les métiers en un seul endroit, c’est-à-dire dans une usine. Nous réduisons ainsi le nombre de déplacements sur les chantiers que ce soient les hommes ou les marchandises », explique Cyril Cosnier, directeur chez HVA Concept. Une fois la douche amenée sur chantier, il n’y a plus qu’à raccorder les toilettes, le siphon de douche et le raccordement électrique.
Du sur-mesure en série
Les salles de bains préfabriquées, connues aussi sous l’appellation « pods », sont maintenant utilisées dans tous les secteurs du marché et à tous les niveaux de prix : logements haut de gamme, logements sociaux, résidences étudiantes, hôtels, hôpitaux, EHPAD… « Pour la douche, la nouvelle réglementation impose le zéro ressaut. Certains acteurs du secteur ont déclaré qu’il faudrait attendre des années avant d’être capable de faire des douches sans fuite car cette norme implique de nombreux corps d’état, ce qui ne garantit pas un résultat sans défaut. Avec la construction hors-site, l’industriel va pouvoir réaliser des prototypes, réaliser des tests et mettre sur le marché un produit accompagné de procédures d’autocontrôle. Il sera ainsi possible de garantir des douches sans fuite », commente Pascal Chazal, CEO du groupe Hors Site. Des freins culturels persistent tout de même comme les interrogations autour de la personnalisation de ce type de solution. La clé de cette personnalisation, parfois complexe à mettre en œuvre dans un ouvrage fabriqué hors-site, réside dans la standardisation et la conception paramétrique. Plus simplement, dans ce type de conception, chaque élément ou chaque système standardisé possède des caractéristiques figées et des caractéristiques paramétrables. À l’échelle d’un système, une pièce pourra avoir une largeur figée et une longueur et un emplacement d’éclairage qui s’adaptera à la longueur du bâtiment. Cette approche permet à l’ouvrage de s’adapter aux besoins des différentes parties prenantes et tout particulièrement à ceux des utilisateurs finaux. Baudet, fabricant et installateur de salles de bains préfabriquées, met par exemple en avant la possibilité de faire du « sur-mesure en série ». « Notre outil de production permet une grande capacité d’adaptation sur les finitions et les dimensions. Il est nous est ainsi possible de du sur-mesure en série. L’entreprise accompagne ses clients sur le volet normatif et se faire force de conseil pour le confort des utilisateurs au quotidien », détaille l’entreprise.
Trois Questions à…
Pascal Chazal - CEO de Hors-site Construction et de l’école Campus Hors-site.
« Il faut laisser l’ère du béton derrière nous »
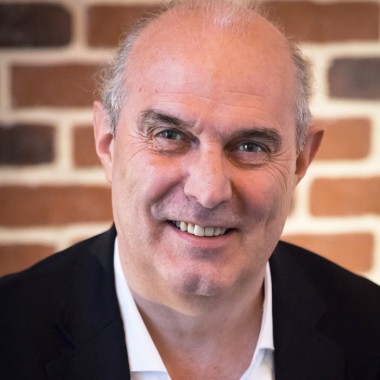
Pascal Chazal : L’objectif est d’arrêter de tout faire sur le chantier, pour fabriquer des éléments et des composants dans une usine. Les avantages sont très nombreux. Le premier est d’apporter de meilleures conditions de travail. Le secteur du Bâtiment est confronté depuis plusieurs années à des problèmes de main d’œuvre et n’arrive plus à attirer les jeunes en partie à cause des conditions de travail sur les chantiers. Le hors-site permet de redonner de l’attractivité à ce secteur en abritant les chantiers sous un toit. Le fait de travailler dans une usine permet d’améliorer la productivité. Entre le déplacement vers le chantier et les aléas des travaux, un ouvrier du bâtiment n’est réellement productif que 20 % de son temps contre 80 % pour un ouvrier travaillant dans une usine dans le secteur automobile. La démarche du hors-site est d’amener les professionnels à un même endroit pour générer encore plus de valeurs. Une meilleure condition de travail et une meilleure productivité engendrent deux autres avantages : la qualité du produit final ainsi que la réduction des coûts. Enfin, le principal atout de la construction hors site est la réduction du bilan carbone d’un projet. Elle permet de favoriser les modes constructifs alternatifs, type ossature bois ou métallique. Mais le hors site pourrait aussi constituer une opportunité pour raisonner en termes de sobriété des matières, en particulier si la hausse du coût des matières premières se poursuit dans le temps. Il peut remplir des objectifs ambitieux de recyclabilité, d’économie circulaire et de limitation des déchets. Cela va dans le sens de la RE2020 quant à la limitation de l’empreinte carbone. Chaque année, le Bâtiment gaspille 1,5 milliard d’euros de matériaux neufs. Les coûts de transport et les accidents sur site sont également grandement réduits. Pour conclure, les chantiers sont terminés plus rapidement grâce à ce mode de construction.
P.C : Le monde du Bâtiment est basé sur l’utilisation massive du béton. Or le béton représente 8% des émissions de GES, c’est plus que l’ensemble de l’aviation mondiale, nous n’avons d’autre choix que de changer et vite ! Le secteur a du mal à changer ses habitudes car le béton est un matériau fantastique qui résout beaucoup de problèmes. Mais aujourd’hui, nous sommes confrontés à un véritable problème environnemental ; il faut laisser l’ère du béton derrière nous. Les bâtiments ont également beaucoup évolué au fil des années. Il y a 40 ans, le gros-œuvre représentait 70 % d’un chantier et 30 % de lots techniques et architectural. Aujourd’hui, c’est l’inverse et cela implique une multiplication des acteurs intervenant sur un projet. Le hors-site se positionne donc comme l’une des principales solutions pour résoudre ces problèmes. Nous devons sensibiliser les pouvoirs publics et les institutions pour démocratiser ce mode de construction. Une prise de conscience est en train de s’effectuer surtout face à l’avancée des autres pays dans ce domaine comme Singapour où le hors-site a été imposé avec un taux de préfabrication de 65 %. L’Angleterre et la Suède ont aussi misé dessus depuis une dizaine d’années pour lutter contre le manque de main d’œuvre. Longtemps, le hors-site s’est révélé plus coûteux que la construction traditionnelle car cette dernière était optimisée au maximum. La tendance est en train de s’inverser à cause des problèmes de recrutement, de la flambée des prix des matériaux et des matières premières. Nous sommes à la croisée des chemins avec une construction hors-site en amélioration continue. Les Suédois ont boosté leur productivité de 30 % en moins de 10 ans. Les principaux acteurs français de la construction ont pris conscience de ce nouveau mode de construction. Bouygues s’est d’ailleurs engagé à réaliser 30 % de construction bois d’ici à 2030.
P.C : Il n’y a pas eu de technologie de rupture. L’évolution concerne principalement les outils de préfabrication depuis une quarantaine d’années avec la robotisation des usines. Néanmoins, un site de production entièrement robotisé n’entraînera pas forcément une baisse conséquente des prix. La rupture se situe au niveau des process en pensant préfabrication plutôt que chantier. À l’image du secteur automobile, il faut désormais créer des équipementiers du bâtiments qui développeront chacun des produits complexes, à forte valeur ajoutée comme des salles de bains, comme des modules avec lesquels on saura faire des logements, des écoles etc. Ces éléments seront ensuite livrés et assemblés rapidement sur le chantier. Des grands changements sont aussi à prévoir pour l’organisation du secteur. Premièrement, les habitudes du bâtiment qui sont de penser prototype pour chaque opération ne sont pas adaptées à l’industrialisation. Il est donc difficile de fabriquer des modules en amont et de les amortir. Nous sommes également confrontés à des organisations segmentées : le maitre d’ouvrage, le maitre d’œuvre, les entreprises professionnelles, les bureaux d’études etc…Tout cela est poussé par la réglementation comme la loi MOP, alors que la construction hors-site regroupe souvent l’ensemble des métiers. Il faut favoriser des processus d’achat qui facilitent la collaboration des acteurs.
Sur le même sujet
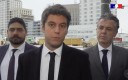
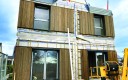
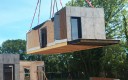
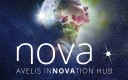
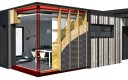